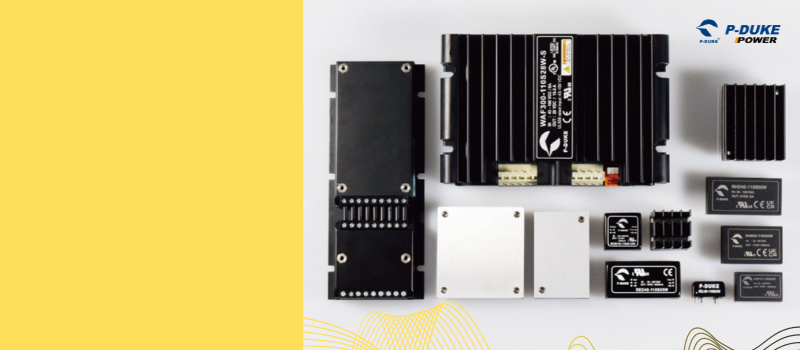
Published on October 31, 2023 - 00:00
How DC-DC Converters Are Used in Railway Systems
Electric mobility systems such as high-speed trains rely on a constant current supply both to power the motors that drive the vehicle and the electrification systems for the control circuits. It is worth remembering that these electric mobility solutions are significantly more energy efficient than any other propulsion system based on fossil fuels such as coal, diesel or gas, while at the same time reducing CO2 emissions.
DC-DC converters play a crucial role in improving the energy efficiency and power quality of electrified railways. The electronic components used within these applications will be subjected to extreme temperatures, humidity, vibrations and mechanical shock conditions. For this reason, they require a high degree of structural integrity to withstand these conditions and operate reliably.
So what are the requirements for DC-DC converters in railway systems and how are they used? Finally, what are the international standards that guarantee their efficiency and reliability?
A look at electric mobility trends and systems
The first railway electrification systems were based on low voltage direct current from which power was supplied through diode rectifiers in traction substations along the track, distributing the power to the train motors through overhead lines and rails. The most common voltages for DC traction systems are 600 V for older trams, 750 V for newer metros and 1500 V for more complex suburban line systems. Some projects of considerable geographical size finally use 3000 V systems to reach even long distances.
The first trend that can be noted is the constant growth in terms of voltage. For the same power, the increase in voltage allows a decrease in current; lower voltage systems will therefore require a higher level of current, with a consequent increase in the cross-section of the cables to be used.
Another trend can be identified in the constant increase in energy efficiency to reduce CO2 emissions. Among the most mature systems are energy reuse systems through regenerative braking, where the kinetic energy of the rotor is converted into electrical energy to be reused by the main engine.
How DC/DC Converters Are Used in Railway Systems
The use of DC/DC converters is central to this particular application category, bringing with it some absolutely important characteristics. In order to ensure correct energy distribution within vehicles such as trains, trams and subways, several series of DC/DC converters are required to supply voltage from primary systems dedicated to movement and secondary systems dedicated to all on-board services. As seen previously, nominal input voltages can vary from a minimum of 24 V to a maximum of 110 V, with a regulated output of 3.3, 5, 12, 15 or 24 V. It is important to remember that the European standard EN 50155 for railway electrical equipment requires that the nominal input voltage can fluctuate between 0.7 and 1.25 times the nominal voltage, with short-term deviations between 0.6 and 1.4 times the nominal input voltage.
From these numbers, we can deduce that a 110V system would require a continuous voltage range of 67V to 120V, and a fluctuation voltage range of 66V to 154V. Digimax's converters support wide input ranges to cover more than one nominal input voltage. For example, P-Duke's RCD series is designed and built to provide ultra-wide input voltage range coverage.
Focusing on real applications, regenerative braking is a prime example of the use of DC/DC converters: these solutions are much more compact than bulky bidirectional converters and can return power to the battery pack or energy storage system from the main power line, or distribute power reliably and continuously to all electronic devices and subsystems within the vehicle. The reliability of auxiliary systems within electric vehicles is also a key consideration, and ensuring the functionality of critical systems such as engine drive controls, braking systems, indicators and warning lights, information displays and door opening and closing systems is truly central.